Plastics Rotational Molding is a manufacturing process used to create hollow plastic parts. The process is ideal for producing large, hollow parts that are sturdy, seamless, and uniform in thickness. It involves heating plastic resin in a hollow mold, which is rotated on two axes until the melted plastic coats the entire surface of the mold. This process leads to an even thickness of the plastic material over the entire object, making it perfect for a range of products. Here is all you need to know about rotational molding.
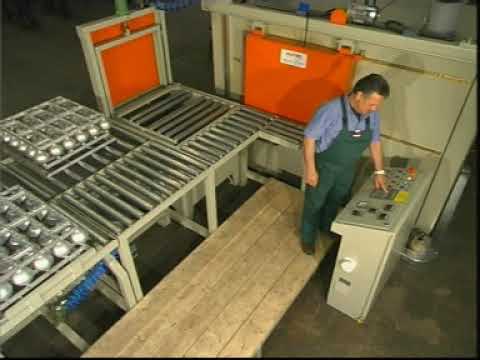
- The Rotational Molding Process:
Rotational molding involves five steps. The first stage of rotational molding involves the production of the mold. This is a crucial step in the process, as the mold must be designed to ensure seamless and uniform plastic distribution. Once the mold is adequately created, the plastic resin is added, and the mold is heated and rotated on two axes. The heating process causes the plastic to liquefy and evenly coat the inside surfaces of the mold. The mold is then cooled, and the plastic solidifies and takes the shape of the interior mold.
- Material Used in Rotational Molding:
Rotational molding is often used with high-density polyethylene (HDPE) and polyvinyl chloride (PVC) resins. These materials are widely available, relatively inexpensive and can be used to produce items ranging from small toy parts to large recycling bins. The availability of these materials also means that there is a wide range of color options and additives that can be used to enhance properties, such as UV resistance, flame retardancy, and wear resistance.
- Advantages of Rotational Molding:
One of the numerous benefits of rotational molding over other plastic molding techniques is that it allows for the production of large, seamless parts with complex shapes. The rotational molding process creates strong, uniform walls with varying thicknesses, which can help to reduce material waste. The design of the mold itself lends itself to geometry, meaning intricate designs can be created with ease. The fact that the process involves a single mold also helps to reduce production costs, particularly for large-scale production runs.
- Applications of Rotational Molding:
Rotational molding is commonly used in the production of large, bulky objects such as tanks, playground equipment, trash cans, and recycling bins. It is also sometimes used in the making of medical equipment, automotive parts, and hunting blinds. Rotomolding is an ideal process for manufacturing multi-wall containers, tanks, and other parts that require varying thicknesses of walls without any seams. It is also an ideal production process for parts that demand a ductile plastic material.
- Maintenance of Rotational Molding Equipment:
To maintain any rotomolding equipment, it is essential to regularly inspect the rotating mechanism of the machine, the oven burners, and the molding chamber. It is also necessary to keep the area surrounding the machines clean and address any spillages or buildup of plastic material, as this can lead to hygiene issues and affect the quality of the finished product.
Rotational molding is one of the most versatile and cost-effective plastic manufacturing techniques. It creates seamless and uniform parts with a range of physical properties. It is an ideal technique for production of parts that require a ductile material such as tanks, playground equipment, and recycling bins, among others. To maintain the rotational molding equipment, it is crucial to regularly inspect and clean the machine. So, if you are looking to manufacture plastic parts, the rotational molding technique is worthy of investigation.